Interview with Camille Breeze, Founder of Museum Textile Services
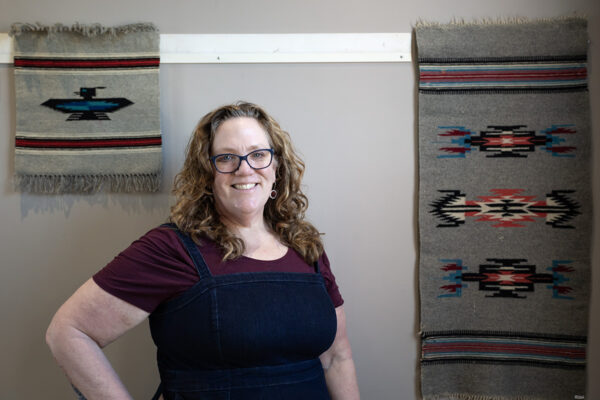
SmallCorp had the opportunity to visit Museum Textile Services (MTS) and chat with its founder Camille Breeze. Museum Textile Services is a full-service textile conservation studio serving private and institutional clients. Museum Textile Services conservation and exhibition collaborations have received awards from the AAM, AASLH, NEMA, and Maine Preservation. Breeze began her conservation career in 1989 at the Textile Conservation Workshop in South Salem, New York, and earned a BA in Art History from Oberlin College. Breeze received an MA in Museum Studies: Costume and Textiles Conservation from the Fashion Institute of Technology. More recently in 2015, she co-founded the Andover Figures® line of custom museum forms for conservators and collection specialists. Breeze is active in many associations and conservation committees and is an instructor at the Center for Collections Care at Beloit College. Breeze’s full bio and CV can be found on the Museum Textile Services website.
Breeze is no stranger to SmallCorp and our products. We’ve enjoyed working with her over the years, and her feedback has been invaluable in terms of improving our products and advising other clients. We sat down to talk to Breeze about some of her favorite SmallCorp products, and why she chooses to use them in her conservation efforts.
SmallCorp: You have been using SmallCorp products for many years now. How did you first hear about us?
Breeze: I began my textile conservation career in 1989 at the Textile Conservation Workshop, where I first learned of SmallCorp. Although that was many years ago, I remember how generous and patient the staff was with me, an emerging professional. I still rely on that same excellent customer service to guide me on how to best use the products you design and manufacture.
SmallCorp: As your company name suggests, textiles are a main focus in your conservation work. What are some of the main reasons an individual or institution seeks out your services?
Breeze: Over the course of any given year, Museum Textile Services receives about 50% of our projects from individual collectors and 50% from museums, historical societies, cultural agencies, the US Park Service, and branches of the military. Individuals come to us with little or no knowledge of conservation and often have a strong sentimental attachment to the items they bring. Larger and small organizations bring a different set of considerations, and often larger volume projects. Our job in every case is to advocate for the textiles and make sure that preservation and display solutions reflect the textile’s needs.
SmallCorp: Are there types of projects you find especially enjoyable or extra rewarding?
Breeze: I spent part of my childhood overseas and I have always liked world textiles for their materials, designs, uses, and even their survival. But I am also a nerd about flags of all types, sizes, and materials. Fewer things are more satisfying than taking a shredded silk GAR flag, stabilizing it, mounting it on an aluminum solid-support panel, and framing it for public display.
SmallCorp: When considering display methods for textiles what are some of the biggest concerns?
Breeze: Displaying a textile, subjects that textile to gravity, environmental factors, and accidental damage. It is the responsibility of the conservator, therefore, to help choose textiles that are suitable for display, along with the display method to use. A short-term exhibit of, say, quilts, can be accomplished using a SmallCorp slat to hang the quilts on walls. When the textile is more fragile or display will be over the course of many months or years, a frame is usually the best solution. The aluminum honeycomb panel is key to providing a rigid, archival surface, which we cover with padding and fabric. More stable textiles can be pressure mounted between UV-filtering acrylic and the padded panel. This has the benefit of being easily reversible, making the frame and panel suitable for another similarly-sized textile. More often, the conservator has to hand stitch a textile to the prepared panel in order for the textile to have sufficient support in the horizontal position. In that case, we employ SmallCorp’s channel fillets as a way to secure the acrylic into the frame before installing the frame a safe distance above the mounted textile. There is no end to the creativity I’ve seen over the years from the SmallCorp crew in creating just the right solution for often-complicated mounting decisions.
SmallCorp: Fellow conservator Gwen Spicer wrote her book Magnetic Mounting Systems for Museums & Cultural Institutions as an in-depth look at the benefits of magnets in Conservation and Exhibition. Do you find yourself integrating magnets in your work?
Breeze: The use of magnets has allowed textile conservators to provide both short- and long-term display solutions with less physical intervention into the textile. At MTS we love the magnetic slat because it is a ready-made solution for quilts and other textiles that already have a hanging sleeve sewn to them. The sleeve is a holdover from the older method of suspending a textile on a rod, and the magnetic slat uses that technology in a way that is adjustable, reliable, and reusable. We also often include magnetic contact points when we mount three-dimensional textiles, such as a Chinese robe, in a SmallCorp frame or shadow box.
SmallCorp: In addition to our magnet slats, we also offer traditional Velcro-based options. What might lead you to choose our Textile Slat or Tube Slat, instead of a Magnet Slat?
Breeze: Having several slat options is a luxury! Our default is usually a Velcro slat that our clients can easily install on a wall and line up with the matching strip of Velcro that is hand stitched to the back-top edge of the textile, with a layer of fabric between. It is safe to store a textile with its Velcro when properly packed. When the client needs that textile to be displayed without a wall, the tube slat is a dramatic solution to suspend a textile from the ceiling. This has the added benefit of allowing both sides to be seen, which is a rare privilege.
SmallCorp: You certainly utilize our aluminum honeycomb panels. We see you frequently using them for mounting flags, like your recent work in Conway, NH on a GAR flag from 1879. I’m curious how this backer assists in the conservation process, both in the short term – the actual installation of the object, and over the long term, while the object is on exhibit or in storage.
Breeze: Before the invention of your aluminum honeycomb panels, conservators mounted textiles on fabric-covered stretchers. The result was a flexible, permeable surface with nothing to inhibit the textile from expanding and contracting, filtering the particulates from flowing air, or being punctured in the event of an accident. The light-weight, sturdy panel can be easily carried and retains the wood perimeter for easily attaching a SmallCorp. powder-coated aluminum frame.
SmallCorp: Do you have a personal favorite between our finished corner aluminum frames or our acrylic box frames? What would make you choose one over the other?
Breeze: The main deciding factor would be the client’s preference for a visual frame around their textile, or a minimally visible floating effect. Both your five-sided acrylic case and your powder-coated aluminum frame with a sheet of acrylic can be used for either a pressure mount or a shadow-box effect where the textile is set back from the acrylic. I have examples of all varieties of your framing solutions in my studio so clients can make informed decisions. I personally am partial to a shadow box made of all-UV-filtering acrylic that stands a few inches off of the textile. This allows the textile to be seen from many angles, which increases the box’s practicality while minimizing its visual impact.
SmallCorp: What made you decide to co-found Andover Figures®, in addition to running Museum Textile Services and working as an instructor at The Center for Collections Care at Beloit College?
Breeze: I was fortunate enough to have moved to Massachusetts in the late 1990s from NYC. After I completed a Mellon Fellowship and wrote a book on tapestry conservation, I chose not to move away for a new job because I love New England. I started my company never expecting it to grow into what it has become 25 years later! Teaching has always been a love for me, and I happily started an internship program at MTS and offered workshops around the region. After I spent every January for ten years leading workshops on archaeological textiles in Peru, I was invited to teach at the Campbell Center for Historic Preservation Studies. When that school closed, my colleague Nicolette Meister, Director of the Logan Museum of Anthropology at Beloit College, founded the Center for Collections Care and invited me to teach textile conservation during summers. Now I look forward to spending a week or so in Wisconsin each summer and I’m excited about the new courses we are developing. I imagine as I reach retirement age, I will concentrate more on teaching and publishing, while my team continues our work at MTS.
SmallCorp: It seems like teaching is a distinct passion for you. Your internship program sounds like a great resource for new conservators and a bridge between your business and teaching. We don’t want to take all your time. Do you have anything else you want to share?
Breeze: Creative problem-solving is my favorite part of my job. So working with SmallCorp, who is dedicated to creating solutions for my industry specifically, means that the sky is the limit when trying to meet both a client’s needs and the needs of their textile. I simply can not imagine being in business for myself if I did not have the solutions and help that SmallCorp provides!
SmallCorp: Thanks for letting us visit and showing us around your workspace!